MEWP stands for Mobile Elevating Work Platform; it’s a broad-ranging term that can be used to refer to a variety of machines, cherry pickers and scissor lifts amongst them. They’re highly versatile pieces of equipment that can be used for an array of applications across a number of different sectors, including construction, warehousing, and repairs and restorations. We should know – we’ve been supplying these machines to the trade for more than 50 years here at Smiths Hire.
Of course, just with any type of heavy-duty equipment, safety is absolutely paramount when deploying and operating MEWPs. Pre-use checks are absolutely crucial for minimising the risk of accidents, which is why every organisation needs a comprehensive pre-use checklist in place. Here are the general items that need including on yours!
Work environment inspection
Before you do anything else, you’ll need to ascertain that the actual area you’re planning to work in is indeed safe. That includes making sure that all hazards are appropriately identified, and (where possible) controlled. Overhead obstructions such as power lines or air conditioning ducts need to be accounted for, and you’ll need to keep an eye out for ground-level hazards too.
Other vehicles can comprise one major obstacle, for example, and special care needs to be taken to ensure the safety of any pedestrians or similarly vulnerable road users who may be moving in and out of the area – whether they’re colleagues or members of the public. Ideally, the immediate working area should be cleared of any surplus tools, equipment or debris, too.
One vital element of a work environment inspection is the ground stability check – essentially, ensuring that the ground supporting the MEWP is solid enough to guarantee that there are no safety issues during usage. Soft surfaces such as soil can sometimes end up settling under heavier loads, which puts the machine at risk of tipping or even overturning entirely. If this scenario can’t be ruled out beyond all reasonable doubt, no work can go ahead until the situation is appropriately remedied.
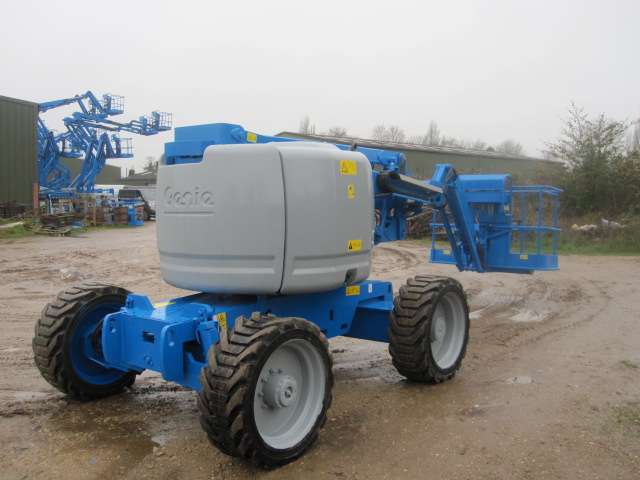
Visual inspection
Once the immediate environment has been made safe, then you can turn your attention to the platform itself. The first thing to check for is any visible signs of damage, wear or corrosion on the machine’s structure or components. All components also need to be properly secured, and you’ll need to double-check that there are no leaks or spills. (Not only can they affect the operation of your equipment, but they can also obviously pose a slipping hazard in and of themselves.)
From there, all signs, labels and operational instructions all need to be clean, clear, and easily legible to the people they’re aimed at. That means operators need to be able to see any internal notices or warnings they’ll need to smoothly and safely operate the machine, and any surrounding pedestrians or drivers need to be able to see external warnings to alert them of potential risks. (For example, warnings that give them some indication of particularly dangerous areas immediately surrounding the MEWP.
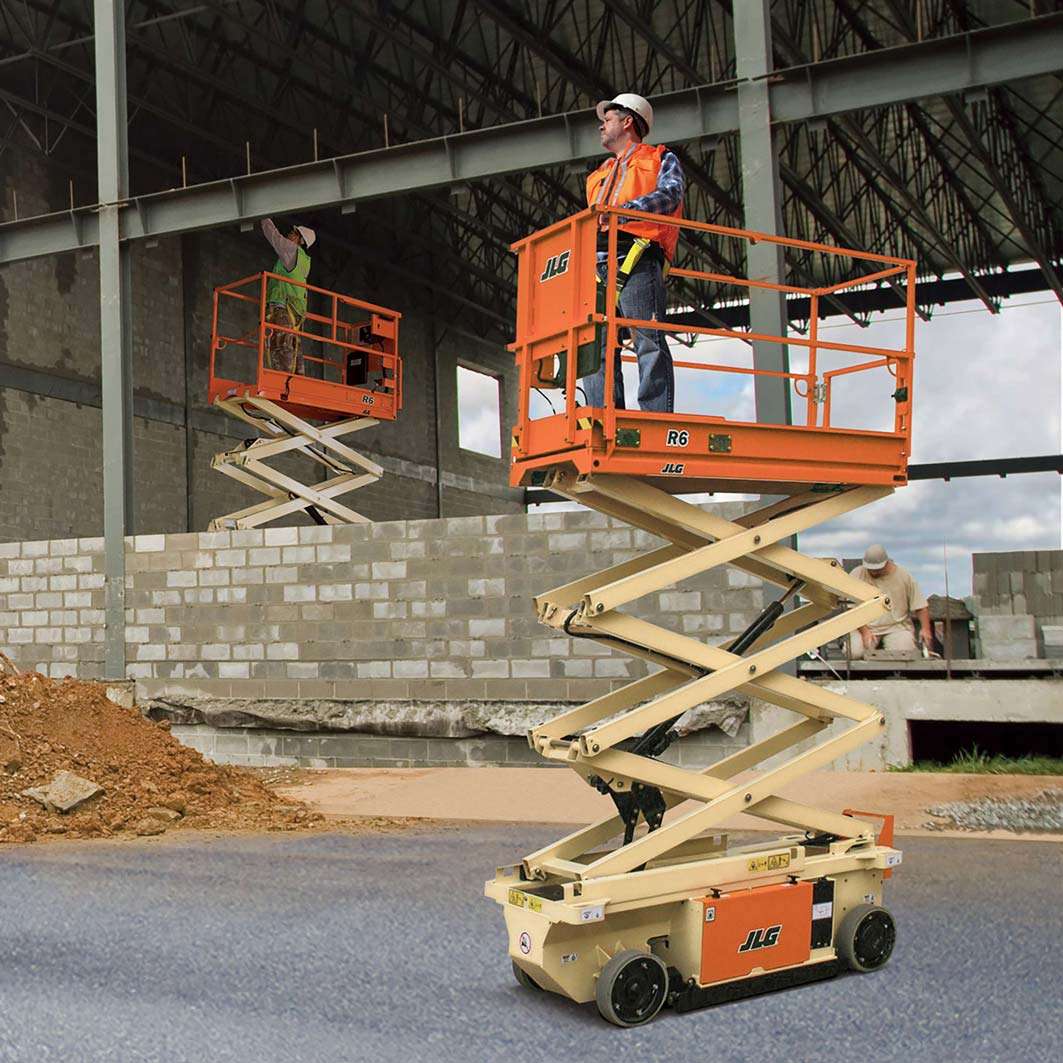
Functional inspection
One of the single most pivotal pre-use checks is, of course, the functional inspection. All ground controls, platform controls and related mechanisms need to be checked to ensure that they’re operating properly, and that there are no leaks, unusual noises, or vibrations on start-up or running.
Safety features also warrant special attention, so make sure to check elements like emergency controls, shutoffs and alarms, and that they’re all functioning perfectly. Only once all key safety elements have been signed off can any work begin.
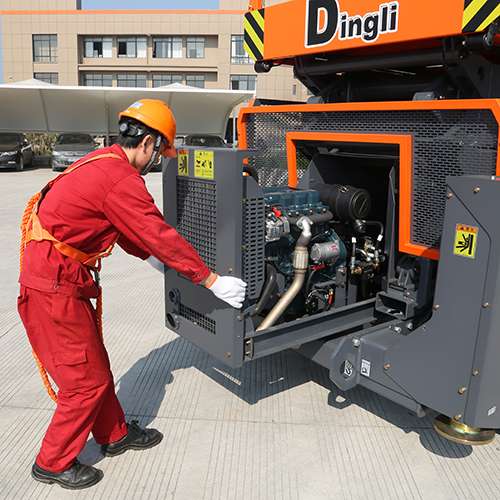
Preparing for emergencies
Once you’ve completed your checks of the MEWP and the surrounding environment, there’s one last thing to finalise. The Work At Height Regulations 2005 legally require employers to have a plan in place for emergencies and rescue when working at height. It’s not enough to simply rely on the emergency services, as it falls under your duty of care as an employer.
For starters, you’ll need to ensure that the ground controls are easily accessible at all times, so that they can be operated by rescuers if necessary. (That means that they can’t be up against a wall, for example.) It’s also worth making sure that several people are familiar with the manual lowering procedure, as it may be necessary to trigger it in the event of a power failure.
Communication is another important aspect. Take care to double check that everyone is aware of the appropriate signals, terminology and protocols that need to be adhered to in the event of an accident or emergency. That includes, for example, the appropriate radio protocol if applicable, as well as key abbreviations or informal shorthand to denote key concepts, equipment, or likely scenarios.
Finally, you’ll need to ensure that you have an appropriate evacuation plan in place, so that you can get yourself and your team to safety in the event of a worst-case scenario. This evacuation plan should encompass designated exit routes, the triggering of alarms, and pre-arranged meeting areas. You may need to run drills if necessary. They’re not everyone’s favourite thing, but they could ultimately make all the difference to someone’s safety.
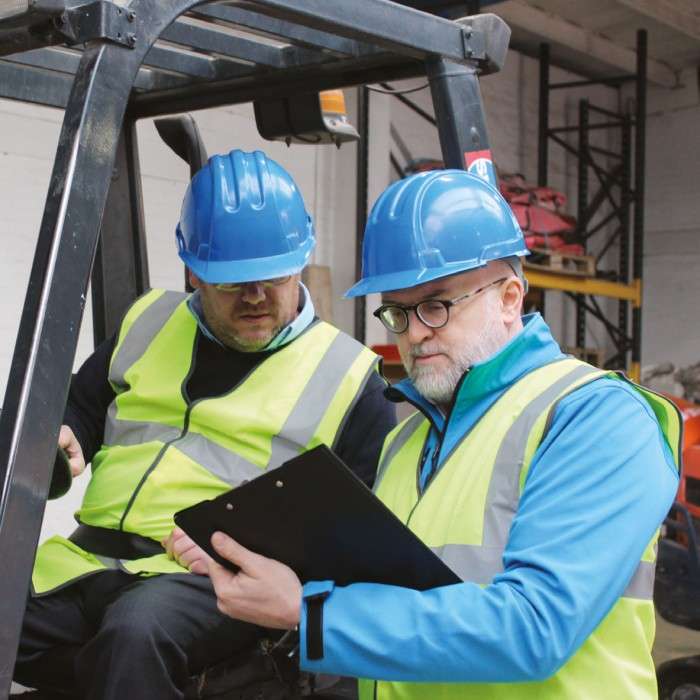
And of course, if you need a quick refresher, you’re in exactly the right place – alongside our extensive range of cherry pickers for hire, we also provide an array of training courses, so you or your team can brush up on key information if you need it.
With courses covering everything from asbestos awareness to counterbalance forklift truck refresher courses, emergency first aid, plant training, safety harness training, and cherry picker and cherry lift training, we cover every type of training to keep your people safe, your equipment in good working order, and your legal health and safety obligations met.
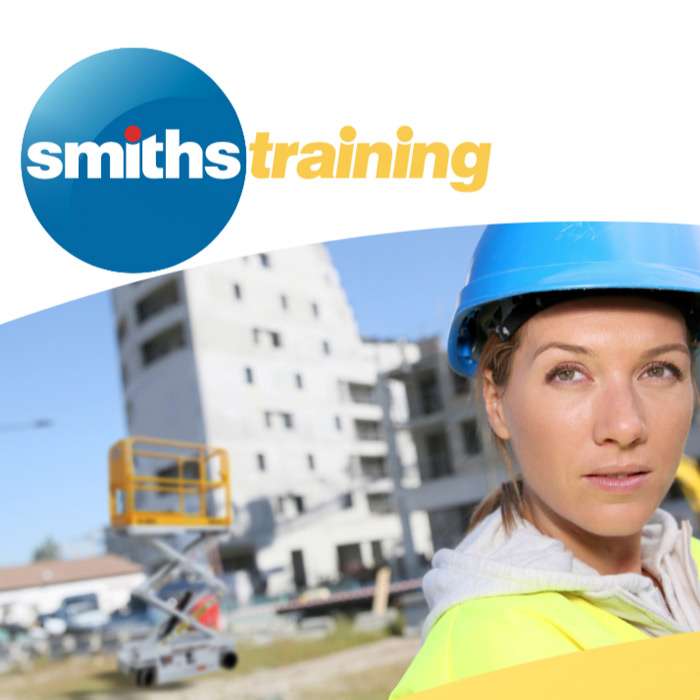
If you have any questions about tool hire or our training courses, don’t hesitate to call our team on 0333 323 2100. We have 17 different tool hire depots and 7 training centres across the North West and Yorkshire, across many major cities, such as Manchester, Liverpool, Preston and Leeds. so we’re confident we can help!